Руководство по химстойким смолам NORPOL
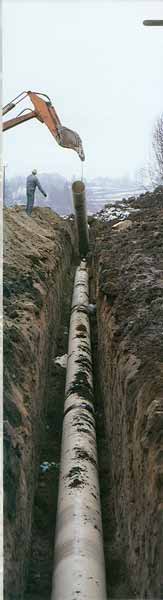
Факторы, воздействующие на эксплуатационные показатели конструкции
Конструкция ламината
Системы отверждения смолы
Контроль качества ламината
Некоторые рекомендации по использованию
Абразивные материалы
Статическое электричество
Питьевая вода и пищевые продукты
Гипохлорид натрия
Диоксид хлора
Бензин / моторное топливо
Скрубберы дымового газа
Озон
Использование инструкций по химстойкости NORPOL / NORPOL DION
Введение
Стойкость к действию химикатов и эксплуатационные показатели NORPOL и NORPOL DION смол продемонстрированы в прошедшие 40 лет успешным использованием разнообразных изделий из композитов в сотнях различных химических средах. Практический опыт был дополнен систематической оценкой соединений, подвергнутых большому количеству химических сред в лабораторных условиях.
Разнообразные коррозионные свойства индустриальных химикалий требуют использования множества составов смол для оптимизации эксплуатационных показателей композитных материалов. Основные типы смол - ортофталевые, изофталевые, терефталевые, бисфенольно - фумаровые и винилэфирные. Каждый тип имеет уникальные преимущества и недостатки, и следовательно важно взвесить все "за" и "против" каждого типа смолы при создании спецификаций смолы. Reichhold может поставлять все химические стойкие типы смол для обычного применения и поможет в оценке ваших определенных требований.
Химически стойкие полиэфирные смолы NORPOL и NORPOL DION бисфенольные и эпоксивинилэфирные смолы обеспечивают в широком диапазоне потребности химических и перерабатывающих отраслей промышленности.
Пульпа и бумага |
Кислоты и щелочи |
Получение энергии |
Обработка стоков |
Нефтехимия |
Рудный процесс |
Металлизация |
Электроника |
Водоснабжение |
Сельское хозяйство |
Фармакология |
Пищевая промышленность |
С конечными продуктами типа:
|
Травильные и гальванические ванны |
Трубопроводы для химикатов |
Сточные коллекторы |
Технологические трубопроводы |
Элементы башенных охладителей |
Стеновые и кровельные системы |
Трубы и скруберы |
Детали вентиляции и футеровки |
Крышки и покрытия |
Решетки и конструкционные профили |
Покрытия пола и растворы |
Факторы, воздействующие на эксплуатационные показатели конструкции.
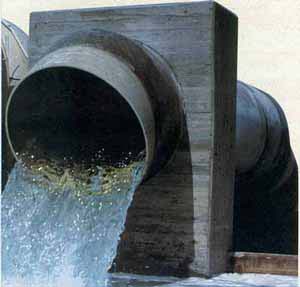
Чтобы получить ожидаемый срок службы конструкции, все следующие показатели важно понимать и использовать правильно.
Отбор правильной Системы Смолы играет важнейшую роль, поскольку различные системы смол имеют различную стойкость к разрушению, вызванному химическим воздействием.
Полиэфирные смолы способны охватить широкий ряд химических воздействий; однако, винилэфирные и бисфенольные смолы выбираются для наиболее агрессивных сред.
Тип армирования будет также влиять на долговременные свойства ламината, поскольку различные стекловолокна показывают различную стойкость к действию химикатов. Отбор типа стекловолокна, стойкого к химической среде, важен для долгосрочной эксплуатации.
Для получения ламината с долгосрочными химстойкими свойствами особенно важно правильно спроектировать и изготовить химстойкий слой. Для этого используются Поверхностные Вуали, изготовленные из химстойких волокон.
Добавление наполнителей, пигментов и / или других добавок к системе смолы также может отрицательно влиять на стойкость к действию химикатов, так что их нужно избегать, когда нужно изготовить ламинат с высокими характеристиками.
Правильная конструкция ламината также существенна, но не только химически стойкого слоя, но также и структурного ламината. Достаточная жесткость должна быть создана, чтобы избежать слишком высоких деформаций в течение срока службы, которые могут привести к появлению микротрещин и последующему разрушению из-за более быстрого химического разъедания.
Оптимальное конструктивное соединение между различными частями ламината должно предохранять от разрушения всю конструкцию. Надлежащее мастерство изготовления ламината должно гарантировать хорошее присоединение частей, создающее интегрированную конструкцию с длительным сроком службы.
Оптимальное отверждение и постотверждение химически стойкого компонента имеют предельную важность для срока службы. Плохое отверждение / слишком низкий уровень сшивающих связей системы смолы при вводе в эксплуатацию определенно уменьшит стойкость к действию химикатов и ожидаемый срок службы изделия.
Поэтому очень важно правильно выбрать температуру отверждения / постотверждения для используемой системы смолы.
Тип армирования, используемого в ламинате, влияет как на краткосрочные, так и на долговременные свойства. Армирующее стекловолокно поставляется разнообразных типоразмеров и составом связки, и даже состав самого стекловолокна может меняться у поставщиков. Эти различия могут проявляться в смачиваемости, стойкости к действию химикатов и физико-механических свойствах и т.д.
Тип и количество армирования прежде всего определяют краткосрочные свойства, такие как физико - механические характеристики. Согласно спецификациям изделия и требованиям должно использоваться армирование, обеспечивающее требуемые свойства. Особенно важно армирование для достижения необходимой жесткости, чтобы избежать дефектов из-за возможной усталостных и высоких нагрузок.
Долговременные свойства, в данном случае стойкость к действию химикатов, также находятся под влиянием выбора армирования. Стекломат из рубленного волокна (CSM), ровинги для напыления, тканые ровинги / мультиосевые ткани, ровинги для непрерывной намотки поставляются различных марок и важно произвести надлежащий выбор.
Поставщики стекловолокна разработали специальные марки для химстойких ламинатов, оптимизировав состав стекла и типоразмеры. Если выбрано неподходящее стеклоармирование, вероятна более быстрая деградация свойств т.к. связь смолы и стекла и, стекло непосредственно, вероятно, разрушится или повредится под воздействием химикатов.
Поверхностная вуаль
Для любого полимерного композита, предназначенного для работы в химически агрессивной среде необходим правильно построенный химстойкий барьер, использующий поверхностные вуали. Существуют поверхностные вуали на основе C - стекла и синтетических волокон.
Вуали из C - стекла широко используются, поскольку они легко укладываются на сложные формы, легко смачиваются и обеспечивают превосходную общую стойкость к действию химикатов.
Синтетические вуали труднее уложить на место и пропитать, но они могут обеспечить более толстый и обогащенный смолой химстойкий слой. Обычно рекомендуются синтетические вуали на основе полиэфирных волокон.
Имеются на выбор различные типы синтетической вуали и, рекомендуется, чтобы они использовались в определенных условиях.
Пожалуйста также консультируйтесь с вашим поставщиком вуали для специальной рекомендации по качеству вуали, поскольку различные химические среды могут требовать специальных синтетических волокон.
Добавки
Любая добавка, добавленная к смоле может уменьшать стойкость к действию химикатов. Тиксотропные системы смолы имеют тенденцию незначительно уменьшать химстойкость, означая что, если эксплуатационные условия очень близки к пределам, заявленным в документации, должна использоваться нетиксотропная версия смолы.
Это также справедливо для смолы с LSE системой. Другие наполнители, введенные в смолу могут катастрофически снизить химстойкость ламината и их нужно всегда избегать.
Для специальных применений, подобно пултрузии, используются так называемых LP смолы. Обратите внимание, однако, что LP добавка, используемая в таких случаях (обычно Поливинилацетат) уменьшит стойкость к действию химикатов.
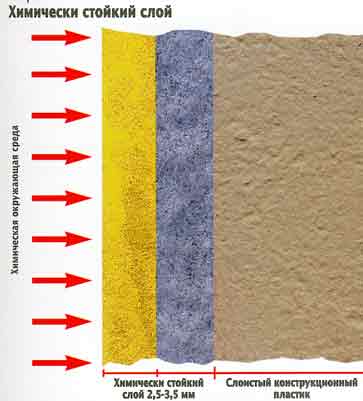
Правильно спроектированный антикоррозионный барьер, использующий поверхностную вуаль, требуется для любого полимерного композита, предназначенного для службы в коррозионной среде. Рекомендуется поверхностная вуаль на основе C - стекла или синтетического полиэфирного волокна. Общая производственная практика - один или два слоя вуали, пропитанные смолой приблизительно на 90%, сопровождаемые минимум 2 слоями 450 g/m2 порошкового стекломата, пропитанного смолой приблизительно на 70%.


После этого химстойкого слоя сооружается несущий ламинат. Тип и количество армирования должны соответствовать требуемым механическим свойствам. Предпочтительно изготовить ламинат из смолы, используемой для химстойкого слоя, однако, хорошая и общепринятая практика, строить основную часть из конструкционного ламината из менее стойкой смолы, например, изофталевой смола с приемлемой Температурой Тепловой Деформации (HDT).
Конструктивное соединение (Приформовка)
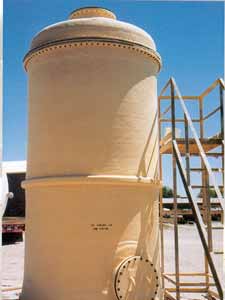
Помните, всегда заканчивайте ламинат рубленным волокном / стекломатом или ровингом и всегда начинайте приформовку с рубленных волокон. Если ламинат заканчивается или приформовка начинается тканым ровингом, вероятность расслаивания ламината очень большая.
При склеивании частей ламината вместе необходимо придерживаться правил по склейке/формованию, описанных в стандартах (таких как BS 4994-87), относительно необходимой зачистки, ширины сужения и перехлеста.
Один из наиболее важных факторов, определяющих стойкость композитов к действию химикатов - это степень отверждения системы смолы.
Ненасыщенная полиэфирная смола / эпоксивинилэфирная содержит ненасыщенные группы в полимерной основе, которые сополимеризуются с мономером стирола в течение процесса отверждения, и формируют устойчивую трехмерную полимерную сеть.
Формирование этой трехмерной сети должно быть завершено; то есть все активные связи в полимерной цепи должны быть сшиты с мономером стирола.
Если произошла неполная сшивка, то не достигается оптимальная степень отверждения и недоотвержденная смолы, подвергнутая воздействию химикалий, вероятно, деструктирует. Поэтому существенно, чтобы использовались хорошие системы отверждения, зачастую специально разработанные для различных типов смолы.
Полиэфирные смолы NORPOL могут поставляться как неускоренные, так и предускоренные.
Предускоренные смолы содержат оптимизированную систему ускорителя, обеспечивая с рекомендуемыми пероксидами хорошее отверждение / сшивку.
Обычно рекомендуется стандартный MEK пероксид. Для неускоренных смол вместе с пероксидом должна использоваться хорошая система ускорителя. Чтобы гарантировать хорошее отверждение / сшивку можно использовать один из специальных NORPOL ускорителей.
Во всяком случае, всегда следуйте за инструкциями поставщика смолы, или консультируйтесь с ближайшим офисом Технической поддержки Reichhold.
Поскольку базовые эпоксивинилэфиры NORPOL DION не ускорены, требуется добавления и ускорителей и пероксидов для управления временем гелеобразования и степенью отверждения.
Критерии выбора системы отверждения и количеств ускоряющих добавок и пероксида зависят от желаемого времени гелеобразования, температур смолы и цеха, толщины ламината, влажности, возможных примесей и возможности постотверждения.
В любом случае, для обеспечения полного отверждения нужно избегать отверждения при температуре ниже 18oC
Рекомендуемые системы отверждения при комнатной температуре для NORPOL Полиэфирных смол:
Октоат Кобальта / MEK Пероксид - Co/MEKP |
Октоат Кобальта /Диэтиленамин/MEK Пероксид -Co/DEA/MEKP |
Октоат Кобальта или Кобальт / Аминовый ускоритель, в комбинации со стандартным MEK Пероксидом, обычно используются для NORPOL полиэфирных смол. Типичные рекомендуемые системы отверждения для неускоренных модификаций - 1-2% NORPOL Ускоритель 9802P + 1-2 % NORPOL Пероксид № 1. Для предускоренных модификаций рекомендуется 1-2 % NORPOL Пероксид №1.
Рекомендуемые системы отверждения при комнатной температуры для NORPOL DION эпоксивинилэфиров:
Октоат Кобальта / Диметиланилин / MEK Пероксид -Co/DMA/MEKP. |
Октоат Кобальта / Диметиланилин /Гидроперекись Кумола - Co/DMA/CHP. |
Диметиланилин / Дибензоил Пероксид / -DMA/BPO. |
Стандартные MEK Пероксиды вызывают пенообразование при использовании с эпоксивинилэфирами, поэтому, для уменьшения пенообразования, разработаны специальные Пероксиды типа NORPOL Пероксид №11 и соответствующие типы других производителей.
Гидроперекись кумола, такая как NORPOL Peroxide №24 и аналоги, не вызывает пенообразования в NORPOL DION эпоксивинилэфирах и, поэтому, хорошо подходит для RTM применений.
Рекомендуемые системы отверждения при комнатной температуре для модифицированных уретаном NORPOL DION эпоксивинилэфиров и модифицированных фумаратом бисфенола, полиэфиров:
Октоат Кобальта / Диметиланилин / MEK Пероксид -Co/DMA/MEKP. |
Диметиланилин / Дибензоил Пероксид / -DMA/BPO. |
Для модифицированных уретаном NORPOL DION эпоксивинилэфиров и модифицированных фумаратом бисфенола, полиэфиров стандартные MEK Пероксиды годны к употреблению, поскольку они не создают вспенивание до отверждения.
Постотверждение при повышенных температурах улучшает свойства композита в некоторых средах. Постотверждение композитов обеспечивает две выгоды: приведение реакции отверждения к завершению максимизирует плотность сшивки системы смолы и устранение непрореагировавших связей в смоле. Это улучшает и стойкость к действию химикатов и физико-механические свойства. Кроме того, полное постотверждение в течении продолжительного периода времени может также уменьшать напряжения, сформированные в ламинате в процессе отверждения, таким образом сокращая вероятность деформаций в течение нормальных тепловых перепадов в процессе эксплуатации. Вообще, можно связывать рекомендуемые температуры постотверждения с характеристиками базовой смолы, используемой в производстве, и это главным образом связано с HDT смолы.
Типичные рекомендуемые температуры и время постотверждения для различных смол, в зависимости от HDT, приведены в следующей таблице:
Температура |
Продолжительность постотверждения, часы |
|||
HDT смолы, оС |
||||
65 |
85 |
100 |
130 |
|
40 |
24 |
48 |
96 |
120 |
50 |
12 |
24 |
48 |
92 |
60 |
6 |
12 |
18 |
24 |
70 |
3* |
6 |
9 |
12 |
80 |
1,5* |
3 |
4 |
6 |
*Постотверждение при температурах выше HDT должно проводиться |
Рекомендуется, чтобы конструкция находилась в течение 16-24 часов при комнатной температуре (>18oC) до начала постотверждения при повышенной температуре. Увеличение и уменьшение температуры должно производиться постепенно, чтобы избежать возможного термоудара и, следовательно, возможных внутренних напряжений.
Долговременные свойства сложной конструкции определяются ее качеством, и не только правильным выбором сырья, но также и качеством изготовления. Возможные дефекты в ламинате могут привести к снижению долговременных свойств, особенно стойкость к действию химикатов, так что необходимо подчеркнуть важность визуального осмотра и контроля при изготовлении до ввода в эксплуатацию.
Внутренняя и внешняя пористость должны быть исключены надлежащим изготовлением и в любом случае обязательно должны быть ниже допустимых по соответствующим стандартам. Если возможно, следует провести ремонт и исправление. Нужно избегать непропитанного армирующего материала, особенно поверхностной вуали и обязательно это должно быть исправлено перед вводом в эксплуатацию.
Внутренние и внешние трещины также должны быть просмотрены, и возможно восстановлены до ввода в эксплуатацию. Допустимые дефекты и методы исправления подробно описаны в известных стандартах по химически стойким изделиям и рекомендуется выполнить эти рекомендации для долговременной службы конструкции.
Степень отверждения, как упомянуто выше, также является важным фактором, управляющим долговременными свойствами. Часто необходим подходящий контроль степени отверждения, чтобы гарантировать эксплуатационные требования. Возможны несколько способов и самый простой - определение твердости поверхности по Barcol. Усредненные данные для ламината, как минимум, должны быть равны значению, указанному для полностью отвержденной неармированной смолы.
Более сложные способы измерения также доступны, типа измерения остаточного содержания стирола и/или измерения остаточной реакционной способности, но такие испытания должны проводиться на образце в специально оборудованной лаборатории. Проконсультируйтесь, пожалуйста, с вашим поставщиком смолы для дальнейших рекомендаций.
В промышленности приходиться встречаться с несколькими различными химикатами и агрессивными средами. Некоторые химические среды и условия требуют специального внимания при изготовлении изделий из стеклопластика.
Композитные трубы и система трубопроводов могут обеспечить значительно лучший ток воздуха и жидкости, по сравнению с обычными материалами, благодаря гладким внутренним поверхностям. Для изделий, предназначенных для жидкого цементного теста и грубых частиц в процессе проектирования должен рассматриваться эффект абразивного износа. Сопротивление истиранию может быть увеличено использованием синтетических вуалей или, для чрезвычайных случаев, использованием карбид кремния или стеклокерамической дроби как наполнителя в поверхностном слое. В некоторых случаях также эффективны упругие футеровки на основе модифицированных эластомером эпоксивинилэфирных смол.
Смолы и стеклопластик являются диэлектриками и в различных системах трубопроводов и т.д. могут накапливаться высокие заряды статического электричества. Такое накопление статического заряда может быть уменьшено использованием проводящих наполнителей, графитовых вуалей или непрерывных углеродистых нитей в поверхностном слое, что необходимо также учитывать в отношении возможного влияния на стойкость к действию химикатов. Проконсультируйтесь, пожалуйста, с вашим поставщиком смолы для дальнейших рекомендаций.
Изделия, используемые для хранения или транспортировки питьевой воды и других пищевых продуктов должны выполнять требования Национальных и/или Международных стандартов / органов надзора. В них часто определяются пределы количества и типа извлекаемых с поверхности ламината химикалий, включая остаточный (непрореагировавший) стирол. Поэтому особенно важно полное мытье и чистка поверхности ламината, а также надлежащее постотверждение.
Значения температуры и времени постотверждения, приведенные в главе "постотверждение" в этих случаях обычно недостаточны, в связи с более строгими требованиями по минимальному остаточному содержанию стирола, в таких случаях необходимы большее время и/или более высокая температура.
Может быть нестабильным веществом, которое разлагается. Эти продукты разложения активно воздействуют на композит через поверхностное окисление. Разложение гипохлорида натрия может быть вызвано чрезмерной температурой, низким уровнем pH и/или ультрафиолетовым облучением. Разложение может быть также вызвано некоторыми примесями на поверхности ламината. Для оптимальной стабильности, растворы гипохлорид натрия могут храниться при температуре не выше 52оC и pH не менее 10.5. Более высокие температуры и/или низкие уровни pH приведут к постепенному разложению гипохлорида натрия и последующей деструкции поверхности композита.
Смолы NORPOL DION могут выдерживать раствор гипохлорида натрия при температурах больше 52оC и уровне pH ниже 10.5, но при этом следует ожидать уменьшения срока службы.
В процессе производства гипохлорида натрия образуется очень агрессивный к композитам раствор. Когда происходит перенасыщение хлором, трудно контролировать температуру и pH, что может значительно уменьшить срок службы композитных реакторов для гипохлорида натрия и может привести к разрушению конструкции.
Ультрафиолетовое излучение также расщепляет гипохлорид натрия. К счастью это легко предотвратить и конструкции, предназначенные для эксплуатации на открытом воздухе должны содержать УФ поглотитель и быть покрыты топкоатом светлого цвета, чтобы оградить раствор гипохлорида натрия от облучения.
В производстве композита или в верхнем слое, предназначенном для контакта с гипохлоридом натрия никогда не должны использоваться тиксотропные добавки на основе кремнезема. При использовании этих добавок наблюдается значительную деструкцию, следовательно, никогда не должна использоваться тиксотропная версия смолы.
Диоксид хлора использовался в течение многих лет для отбеливания древесной пульпы и для дезинфекции воды. Композиты, сделанные с применением высокоэффективных смол, используются с большим успехом в конструкциях, предназначенных для диоксида хлора .
Композиты, изготовленных с применением высокоэффективных смол могут эксплуатироваться в среде Диоксида Хлора 6-12% до 70oC. При этих условиях поверхность смолы может медленно окисляться, и поверхностное окисление обозначено формированием мягкого желтоватого слоя. В некоторых случаях, этот слой образует защитный от разъедания слой для нижних слоев молы. Из-за возможной эрозии, однако, этот слой может быть удален, что приводит к дальнейшему разъеданию. При температурах выше 70оC композитные структуры могут также противостоять разъеданию диоксидом хлора, но следует прогнозировать уменьшенный срок службы.
Обширные заводские испытания продемонстрировали, что конструкции, изготовленные из модифицированных фумаратом бисфенола смол NORPOL DION 6694, имеет высокую стойкость к разъеданию диоксидом хлора, таким образом, эта смола рекомендуется для таких применений.
Композиты несколько лет успешно использовались для наземных и подземных бензиновых резервуаров. Однако, под давлением требований о повышении чистоты горючего состав бензина изменился. Устранение тетраэтила свинца привело к увеличению в составе бензинов в пропорции ароматических веществ. Использование эфира третичного бутила (MTBE) и других насыщенных кислородом добавок типа этилового и метилового спиртов и третично - аминдиметилового эфира (TAME) может увеличиваться и в будущем.
Использование насыщенных кислородом добавок и повышенные уровни ароматических веществ потребовали смол, которые обеспечивают улучшенную стойкость к действию химикатов по сравнению с изофталевыми смолами, которые обычно использовались. Метанольная устойчивость ламината выдвинулась на первый план в последние годы, поскольку количество метанола, содержащегося в бензине, увеличилось и, следовательно, должна быть принята во внимание для производства бензиновых резервуаров. Из проверенных многочисленных полиэфирных и эпоксивинилэфирных смол, согласно различным стандартам и испытаниям на производительность, можно предложить рентабельные решения на основе высоко сшитых терефталевых смол типа серии NORPOL 640.
Композиты широко использовались в трубах, скрубберах и футеровках вытяжных труб, открытых диоксиду серы и сернистому триоксиду. Смолы с высокими температурными свойствами обычно выбираются, чтобы соответствовать возможным температурным отклонениям, которые могут происходить, если имеется перебои в подаче охлаждающей воды, и при пусковом цикле . Если происходит температурное отклонение, то возможны внутренние поверхностные крекинги из-за большого различия в тепловом расширении внутренней облицовки и остальной части сборной конструкции. Поэтому, тщательное управление и регулирование температуры в процессе пуска и эксплуатации очень важно, также как и регулярные осмотры поверхности. Возобновление футеровки может быть необходимо, если возник внутренний крекинг. Должным образом разработанные композитные структуры могут противостоять кратким температурным скачкам до 175oC без серьезного ухудшения структурных свойств, и могут работать в до 104oC в непрерывном режиме.
Используется обычно, чтобы обрабатывать воду, содержащую канализационные или химические отходы, а также используется при отбеливании и выборочном удалении лигнина пульпы. В этом контекста озон считается "дружественным природе", и его использование, как ожидается, увеличится.
Озон обладает выдающимся окислительным потенциалом, в результате чего он известен как один из наиболее мощных окислителей. Даже при концентрациях менее 4 ppm (~ 4*10-4 %) в воде, озон высоко активен и может воздействовать на поверхность композита, приводя к постепенному разрушению.
В то же время как опыт с уровнем озона в 4 ppm указывает, что разумный срок службы может ожидаться для эпоксивинилэфиров, при более высоких концентрациях. Серьезное поверхностное окисление и эрозия может происходить быстро, требуя частого осмотра и возможного возобновление футеровки.
Озон также очень активен в газообразной форме. В резервуаре, где содержится озоносодержащая вода, испарение озона может вызвать серьезную коррозию в частях, которые не заполнены водой. Поэтому важно гарантировать, что концентрация озона в атмосфере внутри резервуара сохраняется настолько низкой насколько возможно. Стандартные смолы NORPOL не рекомендуется для применений, где присутствует озон.
Для изделий, изготавливаемых методом пултрузии, или других формованных изделий, в которых достигается высокое содержание наполнителя и/или стеклоармирования, или для любого другого процесса производства, при котором не происходить формирование обогащенной химстойкой смолой поверхности, невозможно спрогнозировать поведения композита в агрессивных химических средах. Пожалуйста, свяжитесь с ближайшим офисом Технической Поддержки для специальных рекомендаций.
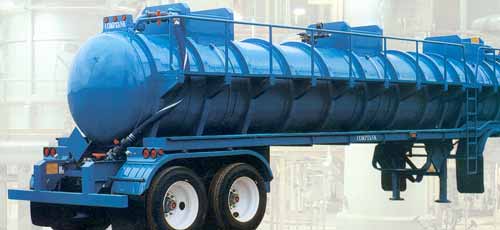
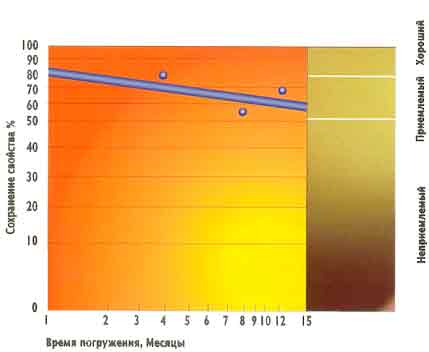
Стандарт ASTM С 581 был создан, чтобы помочь определить, имеется ли ухудшение свойств термореактивной смолы, если слоистый пластик погружен в коррозионную среду. Данные, полученные при лабораторных испытаниях, выполненных в соответствии с ASTM С 581, подтверждаются данными долговременного воздействия коррозионной среды, а также опытом, накопленным в промышленности.
Скорость снижения механических свойств уменьшается со временем почти по логарифмической кривой. После нанесения на график первых данных о сохранении механических свойств изделия, можно достроить прямую, предсказывающую сохранение его механических свойств в зависимости от времени.
Изменения
Изготовитель оставляет за собой право вносить в настоящее руководство по стойкости к действию химикатов изменения без специального уведомления, чтобы обеспечить наиболее современные данные. Изменения могут затрагивать предложенную рабочую температуру или ограничения концентрации
Использование данных
Данные, указанные в настоящему Руководству по химстойкости основаны на результатах для базовых модификаций смолы. Каждая из этих смол, однако, может быть поставлена в базовой, тиксотропной, предускоренной и LSE модификациях, в зависимости от применяемого при производстве стеклопластика процесса.
Химическая среда |
% |
NORPOL DION |
|||||
6694 |
9100/ 9102/ 9300 |
9400 |
9700 |
9800 |
|||
Nitric Acid |
азотная кислота |
2 |
100 |
70 |
80 |
|
90 |
Nitric Acid |
азотная кислота |
5 |
80 |
65 |
70 |
|
80 |
Nitric Acid |
азотная кислота |
15 |
65 |
50 |
55 |
|
65 |
Nitric Acid |
азотная кислота |
35 |
60 |
40 |
50 |
|
|
Nitric Acid |
азотная кислота |
50 |
45 |
НР |
27 |
НР |
45 |
Nitric Acid |
азотная кислота |
пары |
80 |
|
80 |
80 |
|
Gasoline, Regular Unleaded |
бензин неэтилированный |
100 |
|
27 |
40 |
|
|
Gasoline, Alcohol Containing |
бензин спиртосодержащий |
100 |
|
|
40 |
|
|
Gasoline, Regular Leaded |
бензин этилированный |
100 |
45 |
45 |
50 |
|
45 |
Benzene |
бензол |
100 |
НР |
НР |
40 |
НР |
НР |
Vinyl Acetate |
винилацетат |
ВСЕ |
НР |
НР |
20 |
|
НР |
Vinyl Toluene |
винилтолуол |
100 |
|
27 |
40 |
|
НР |
Wine |
вино |
ВСЕ |
|
|
|
|
|
Water, Deionized |
вода, деионизированная |
ВСЕ |
100 |
80 |
90 |
90 |
80 |
Water, Destilled |
вода, дистиллированная |
ВСЕ |
100 |
80 |
90 |
90 |
80 |
Water, Sea |
вода, морская |
ВСЕ |
100 |
100 |
100 |
100 |
100 |
Hydraulic Fluid |
гидравлическая жидкость |
100 |
80 |
65 |
80 |
80 |
65 |
Sodium Hypochlorite 1,2,5 |
гипохлорит натрия |
0-15 |
50 |
50 |
50 |
50 |
50 |
Chlorine Dioxide 1,2,5 |
двуокись хлора |
|
70 |
70 |
70 |
70 |
70 |
Kerosene |
керосин |
100 |
100 |
80 |
80 |
80 |
80 |
Diesel Fuel |
легкое дизельное топливо |
ВСЕ |
100 |
80 |
100 |
90 |
80 |
Fuel Oil |
мазут |
100 |
100 |
80 |
100 |
90 |
80 |
Mineral Oils |
минеральные масла |
100 |
120 |
100 |
120 |
100 |
100 |
Motor Oil |
моторное масло |
100 |
120 |
100 |
120 |
100 |
100 |
Urea |
мочевина |
ВСЕ |
75 |
65 |
65 |
65 |
65 |
Ozone (< 4 ppm in water phase) |
озон (менее 4 ppm в воде) |
|
27 |
27 |
|
|
27 |
Vegetable Oils |
растительное масло |
ВСЕ |
120 |
100 |
80 |
100 |
90 |
Sulfuric Acid |
серная кислота |
0-25 |
120 |
100 |
100 |
100 |
90 |
Sulfuric Acid |
серная кислота |
26-50 |
120 |
80 |
80 |
80 |
90 |
Sulfuric Acid |
серная кислота |
51-70 |
80 |
80 |
80 |
80 |
90 |
Sulfuric Acid |
серная кислота |
71-75 |
50 |
50 |
50 |
50 |
45 |
Sulfuric Acid |
серная кислота |
76-93 |
НР |
НР |
НР |
НР |
НР |
Sulfuric Acid |
серная кислота |
пары |
120 |
100 |
90 |
100 |
90 |
Sulfuric Acid/ Ferrous Sulfate |
серная кислота/ сульфат железа |
10/насыщ |
100 |
90 |
90 |
|
90 |
Sulfuric Acid/ Phosphoric Acid |
серная кислота/ фосфорная кислота |
10/20 |
80 |
80 |
80 |
|
80 |
Brown Stock (pulp mill) |
стоки целлюлозного производства |
|
80 |
80 |
80 |
|
80 |
White Liquor (pulp mill) |
сульфатная варочная жидкость |
ВСЕ |
|
80 |
80 |
80 |
80 |
Crude Oil, Sour or Sweet |
сырая нефть |
100 |
120 |
100 |
120 |
100 |
100 |
Vinegar |
уксус |
ВСЕ |
100 |
100 |
100 |
100 |
90 |
Acetic Acid |
уксуская кислота |
0-25 |
100 |
100 |
100 |
100 |
100 |
Acetic Acid |
уксуская кислота |
25-50 |
80 |
80 |
80 |
80 |
80 |
Acetic Acid |
уксуская кислота |
50-75 |
60 |
60 |
60 |
60 |
60 |
Hydrochloric Acid |
хлористоводородная (соляная) кислота |
10 |
100 |
100 |
120 |
100 |
90 |
Hydrochloric Acid |
хлористоводородная (соляная) кислота |
15 |
100 |
100 |
100 |
100 |
90 |
Hydrochloric Acid |
хлористоводородная (соляная) кислота |
25 |
65 |
70 |
70 |
70 |
65 |
Hydrochloric Acid |
хлористоводородная (соляная) кислота |
37 |
45 |
45 |
45 |
60 |
45 |
Cyclohexane |
циклогексан |
100 |
50 |
50 |
65 |
65 |
|
Cyclohexanone |
циклогексанон |
100 |
НР |
НР |
40 |
НР |
НР |
Ethyl Alcohol (Ethanol) |
этиловый спирт (этанол) |
10 |
65 |
50 |
65 |
65 |
60 |
Ethyl Alcohol (Ethanol) |
этиловый спирт (этанол) |
50 |
50 |
40 |
50 |
|
40 |
Ethyl Alcohol (Ethanol) |
этиловый спирт (этанол) |
95-100 |
50 |
27 |
40 |
|
27 |
НР - Не Рекомендуется,1рекомендуется система отверждения DMA/BPO, 2рекомендуется двойной слой синтетической вуали, 3рекомендуется двойной слой вуали С-стекла, 4рекомендуется вуаль из С-стекла и |
Гарантия
Мы гарантируем, что наша продукция соответствует нашим письменным характеристикам. Ни одно из положений настоящего документа не должно рассматриваться как какая-либо другая гарантия, выраженная или подразумеваемая, например гарантия товарных качеств или применения для определенной цели, а также защиты от какого-либо закона или патентных прав. Все права защищены. Единственное решение при всех обоснованных претензиях - это замена наших материалов, и мы ни в коем случае не несем ответственности за специально или случайно нанесенный ущерб или его последствия.